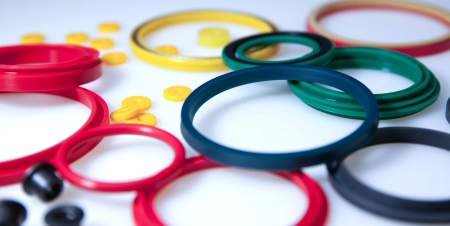
- Manufacturing
- Case Study
Panthera optimises the efficiency of ATP processes
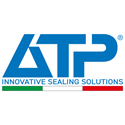
This choice considered not only the product itself, but also reliability of the partner. In particular, Panthera is an innovative and yet reliable and well-established tool, with great functional completeness and able to grow in step with the company, featuring everything needed to support international relationships. On the partner side, the company has chosen a manufacturer able to invest, with a network of certified local partners, but with guarantees direct support and care from the headquarters
Adopting Panthera has enabled ATP to improve the service it offers its customers. A case in point is food certification, for which the previous system provided management of codes but not of batches, thus requiring the use of notes on production orders and tags in storage locations. However, the new European MOCA regulation, also known as 1935/2004, has made the traceability of every object and material in contact with foodstuffs compulsory, including - as an example - many of the gaskets made. Today, thanks to Panthera, ATP is able to trace the origin code of the semi-finished products used in the production of the batch with just a few clicks, which is automatically marked both on the shipping documents and packaging labels accompanying our products. The tangible results, in terms of tracking and traceability, management of various units with coordinated and transparent processes, optimisation of handling and real-time cost control, have enabled management to put Panthera at the heart of the processes, constantly optimising efficiency and investing in organisation and computerisation. Thanks to the gradual computerisation of processes and functions, the initial 15 users have now grown to more than 50, in addition to the production operatives.
ATP is now equipped with most of Panthera's modules, but the investment will not stop as new modules and functions are being developed all the time. An Advanced Logistics project is planned for the immediate future, and once again Panthera can offer an integrated WMS module.